Stainless Steel, Austenitic Group, Ferritic Group, Martensitic Group, Stainless Steel Strip, Intercept® Ultra Stainless
Group Breakdowns and technical specifications for Austenitic, Ferritic, and Martensitic categories listed below are available for download.
STAINLESS STEEL
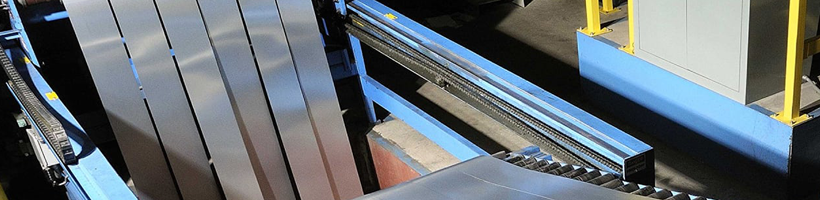
Stainless steel is the name given to a group of corrosion resistant and high temperature steels. Their remarkable resistance to corrosion is due to a chromium-rich oxide film which forms on the surface. When ordinary carbon steel is exposed to rain water, for example, it corrodes forming a brown iron oxide, commonly called rust, on the surface. This is not protective and eventually the entire piece of steel will corrode and be converted to rust. But when enough chromium (more than about 10%) is added to ordinary steel, the oxide on the surface is transformed – it is very thin, virtually invisible and protective in a wide range of corrosive media. This is what we call stainless steel and there are several different types, and many different grades.
The manufacture of quality stainless steel, from heat to heat and year to year, demands precise control of raw material ingredients and melting practices. Exact quantities of presorted scrap and alloying elements are delivered to the mills’ melting furnaces so that the heats or lots will be within specified composition ranges. Those composition ranges typically include a group of chemical elements for each grade of stainless steel.
AUSTENITIC GROUP
This group contains chromium and nickel and is identified by the Type 300 series. Grades containing chromium, nickel and manganese are Type 200. These two types have different compositions and properties, but many common characteristics. They can be hardened by cold working, but not by heat treatment. In the annealed condition, all are essentially nonmagnetic. They have excellent corrosion resistance and unusually good formability. Type 304 (18% chromium – 8% nickel) and Type 316 (16% chromium – 10% nickel – 2% molybdenum) are the most widely used grades in this group.
FERRITIC GROUP
The ferritic stainless steels are identified by the Type 400 series. They cannot be hardened by heat treatment. They are straight chromium alloys and only moderately hardened by cold working. This group is magnetic and has good ductility and resistance to corrosion. Type 430 (16% chromium) is the general purpose stainless steel of the ferritic group.
MARTENSITIC GROUP
This group is also identified by the Type 400 series and are hardenable by heat treatment. They are magnetic and resist corrosion in mild environments. The ductility of this group is fair to good. Type 410 (11.5% chromium) is the most widely used alloy of this group.
STAINLESS STEEL STRIP PRODUCTION & FINISHES
Hot rolled stainless steel strip is a semifinished product obtained from the hot rolling of slabs or billets and is produced for conversion by cold rolling.
Cold rolled stainless steel strip is manufactured from hot rolled, annealed and pickled strip by cold rolling on polished rolls. Depending on the thickness desired, the cold rolling requires various numbers of passes through the mill to effect the necessary reduction and to secure the desired surface characteristics and mechanical properties.
Only three rolled (unpolished) finishes (No. 1, No. 2 and bright annealed) and one polished finish (mill buffed) are commonly supplied on stainless steel strip.
If a customer wishes to have strip polished to finish similar to those for sheet, such as a No. 4 finish, arrangements for this are made with an independent metal finisher; or if the volume is sufficiently high, the customer can install his own finishing equipment. Finishes for strip other than the four mentioned above, usually are not provided by stainless steel producers.
INTERCEPT® ULTRA STAINLESS
Berlin Metals has been a supplier of stainless steel “Ultra” and tinplate coil for the Intercept lines for over 20 years.
Working closely with the machinery manufacturer and our world class mill supplier, we developed the Intercept Ultra Stainless material to meet the demanding requirements of the manufacturing process, minimize die wear and adjustments, and insure your product’s structural integrity. This custom engineered Stainless Steel Alloy Spacer System delivers excellent warm-edge performance at a superior value.