Cold Rolled Strip & Sheet Products
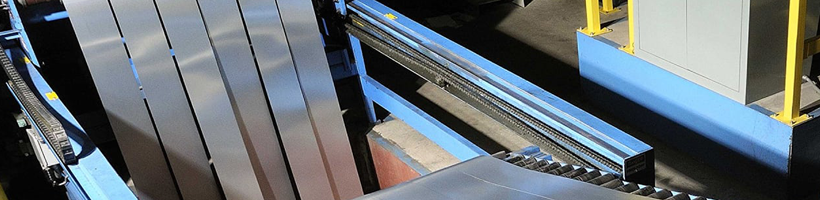
Cold rolled sheet products have been available for many years and are used for a multitude of applications such as appliances – refrigerators, washers, dryers, and other small appliances, automobiles – exposed as well as unexposed parts, electric motors, and bathtubs. Today’s cold rolled sheet products are much improved over those used in the past. They offer better control of thickness, shape, width, surface finish, and other special quality features that compliment the emerging need for highly engineered end use applications. To meet the various end use requirements, cold-rolled sheet products are metallurgically designed to provide specific attributes such as high formability, deep drawability, high strength, high dent resistance, good magnetic properties, enamelability, and paintability.
The first step in manufacturing Cold Rolled Sheet Products involves cold reducing coils of hot-rolled, pickled product to a thinner thickness. The primary feature of cold reduction is to reduce the thickness of hot-rolled coils into thinner thicknesses that are not generally attainable in the hot rolled state. The cold reduction operation induces very high strains (work hardening) into the sheet; thus, the sheet not only becomes thinner, but also becomes much harder, less ductile, and very difficult to form. However, after the cold-reduced product is annealed (heated to high temperatures), it becomes very soft and formable. In fact, the combination of cold reduction and annealing lead to a refinement of the steel that provides very desirable and unique forming properties for subsequent use by the customer.
The hot-rolled, pickled coils incoming to the cold reduction mill have to have excellent quality attributes. The pickling operation must be well-controlled to assure that all the oxides formed during hot rolling are removed. The thickness of the hot-rolled strip is important in that the properties of the final cold rolled and annealed product is influenced by the percent of cold reduction. This means that the thickness of each hot-rolled coil is carefully controlled to provide the mill with a specific thickness to achieve the proper percent cold reduction. Among other things, the percent of cold reduction affects the forming behavior of the product after annealing.
The production of a specific thickness of cold rolled sheet to meet an end user’s requirements involves sophisticated processing from the melt stage forward. Steel chemistry, hot strip mill processing variables, pickling practices, cold-rolling mill practices, annealing practices, and finally, temper rolling practices all have a role in achieving the manufacture of top quality cold-rolled sheet products. This product is manufactured for a large number of applications that require a variety of properties from fairly simple to very sophisticated. The product is typically available at thickness as low as 0.0142 inch although lighter gauges may be ordered. Typically, thicknesses lighter than .015” are ordered as Black Plate.
Cold Rolled Strip Temper Chart
Temper | Under Thickness (In) | Through Thickness (In) | Minimum Rockwell Hardness | Maximum (Approx.) Rockwell Hardness |
---|---|---|---|---|
No. 1 (hard) | 0.025 | . . . | 15T90 | . . . |
0.040 | 0.025 | 30T76 | . . . | |
0.070 | 0.040 | B90.0 | . . . | |
0.250 | 0.070 | B84.0 | . . . | |
No. 2 (half-hard) | 0.025 | . . . | 15T83.5 | 15T88.5 |
0.040 | 0.025 | 30T63.5 | 30T73.5 | |
0.250 | 0.040 | B70.0 | B85 | |
No. 3 (quarter-hard) | 0.025 | . . . | 15T80 | 15T85 |
0.040 | 0.025 | 30T56.5 | 30T67 | |
0.250 | 0.040 | B60 | B75 | |
No. 4 (skin-rolled) | 0.025 | . . . | . . . | 15T82 |
0.040 | 0.025 | . . . | 30T60 | |
0.250 | 0.040 | . . . | B65 | |
No. 5 (dead-soft) | 0.025 | . . . | . . . | 15T78.5 |
0.040 | 0.025 | . . . | 30T53 | |
0.250 | 0.040 | . . . | B55 |
MECHANICAL PROPERTIES
The table below shows the approximate mechanical properties corresponding to the five commercial tempers of cold-rolled carbon steel strip. This table is presented as a matter of general information. The limits of tensile strength, etc., are not intended as criteria for acceptance or rejection unless specifically agreed to by the manufacturer when accepting the order. The exact processing by different manufacturers will naturally vary slightly, so that absolute identity cannot be expected in their commercial tempers of cold-rolled strip.
Approximate Mechanical Properties Table
For Various Tempers of Cold-Rolled Carbon Strip
Temper | Tensile Strength, A | Elongation In 2 In. (50 Mm) For 0.050 In. (1.27 Mm) Thickness Of Strip, B % | Remarks |
---|---|---|---|
No. 1 (hard) | 90 000 ± 10 000 [ 620 ± 70 ] | . . . | A very stiff, cold-rolled strip intended for flat blanking only, and not requiring ability to withstand cold forming. |
No. 2 (half-hard) | 65 000 ± 10 000 [ 450 ± 70 ] | 10 ± 6 | A moderately stiff cold-rolled strip intended for limited bending. |
No. 3 (quarter-hard) | 55 000 ± 10 000 [ 380 ± 70 ] | 20 ± 7 | A medium soft cold-rolled strip intended for limited bending, shallow drawing and stamping. |
No. 4 (skin-rolled) | 48 000 ± 6 000 [ 330 ± 40 ] | 32 ± 8 | A soft ductile cold-rolled strip intended for deep drawing where no surface strain or fluting is permissible. |
No. 5 (dead-soft) | 44 000 ± 6 000 [ 300 ± 40 ] | 39 ± 6 | A soft ductile cold-rolled strip intended for deep drawing where stretcher strains or fluting are permissible. Also for extrusions. |
Note 1 These values are given as information only and are not intended as criteria for acceptance or rejection. S.I. units appear in brackets.
A Tensile properties are based on the standard tension-test specimen for sheet metals, see appropriate figure in Test Methods and Definitions A 370.
B Elongation in 2 in. (50 mm) varies with thickness of strip. For Temper No. 5, dead-soft temper, the percentage of elongation = 41 + 10 log ” t’ ( t = thickness, in. (mm)).
Other tempers vary in a similar way.
†
Editorially changed from ksi to psi.
Typical Ranges of Properties
Mechanical Properites A & Non-Mandatory B
For Cold Rolled Steel Sheet Designations CS, DS, DDS, and EDDS
Designation | Ksi Yield Strength C | MPa Yield Strength C | Elongation In 2 In. [50 Mm ]% C | Rm Value D | N-Value E |
---|---|---|---|---|---|
CS Types A, B, and C | 20 to 40 | [140 to 275] | >=30 | F | F |
DS Types A and B | 22 to 35 | [150 to 240] | >=36 | 1.3 to 1.7 | 0.17 to .22 |
DDS | 17 to 29 | [115 to 200] | >=38 | 1.4 to 1.8 | 0.20 to .25 |
EDDS | 15 to 25 | [105 to 170] | >=40 | 1.7 to 2.1 | 0.23 to .27 |
A These typical mechanical properties apply to the full range of steel sheet thicknesses. As the sheet thickness decreases, the yield strength tends to increases, the elongation decreases and some of the formability values tend to decrease.
B The typical mechanical property values presented here are nonmandatory. They are provided to assist the purchaser in specifying a suitable steel for a given application. Values outside of these ranges are to be expected.
C Yield Strength and elongation are measured in the longitudinal direction in accordance with ASTM Test Methods A 370.
D Average plastic strain ratio (rmvalue) as determined by ASTM Test Method E 517.
E The strain hardening exponent (n-value) as determined by ASTM Test Method E 646.
F No typical properties have been established.
COLD ROLLED STRIP STEEL FINISHES
Cold-rolled strip steel finishes are usually specified to one of the finishes below.
- Number 1 or Matte (Dull) Finish: A finish without luster produced by rolling on rolls roughened by mechanical or other means. This finish is especially suitable for paint adhesion. It also aids in drawing by reducing the amount of contact and therefore the friction between the die and the steel surface. Additionally, lubricating fluid will more easily adhere to the rougher surface this type of finish.
- Number 2 or Regular Bright Finish: Produced by rolling on moderately smooth rolls. It is a suitable for many requirements, but not generally applicable to bright plating.
- Number 2 1/2 or Better Bright Finish: A smooth finish suitable for those plating applications where high luster is not required.
- Number 3 or Best Bright Finish: Generally of high luster produced by special rolling practices, including the use of specially prepared rolls. It is the smoothest and most difficult finish to produce and is particularly suited for bright plating. The production of this finish requires extreme care in processing and extensive inspection. Paper interleaving is frequently used for protection.
Typical Surface Roughness (Ra) Ranges
For each of above finishes are included in the table below. The end user and the steel supplier (producer) should agree on the “aim to” or permissible surface roughness range, based on the intended application.
TYPICAL SURFACE ROUGHNESS RANGES* | |
---|---|
Number 1 or Matte (Dull)** | Ra 20-80 uin. |
Number 2 or Regular Bright*** | Ra 20 uin max. |
Number 2 1/2 or Better Bright*** | Ra 10 uin max. |
Number 3 or Best Bright*** | Ra 4 uin. max. |
*: Due to vagaries in measuring surface roughness, as well as inherent variability in such cold rolled services, these values are only typical and values outside these ranges would not be considered unexpected.
**: Measured either parallel with or across rolling direction
***: Measured across the rolling direction